|
 |

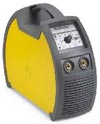 |
 |
RAINBOWS represent the latest evolution in inverter technology DC welding equipment. These powerful 100 KHz power sources are based on latest generation IGBT’s and fitted with a flat transformer.
RAINBOWS, with their lightness, reduced size and their excellent characteristics in electrode (MMA) and TIG welding with "lift" mode arc striking, are the most suitable solution for maintenance and light fabrication works.
Features:
- Reduced weight and size, easy-to-carry
- Innovative and compact design
- Shock-proof plastic main structure
- Control panel protected against accidental impact
- Robust handle built-in into the chassis
- Excellent welding characteristics with any type of electrode
- Low energy consumption and high electrical efficiency
- Automatic compensation for mains voltage fluctuations within + 15% – 20%
- 3 available welding processes: MMA - CrNi - TIG
- Built-in Arc Force to automatically select the best welding arc dynamic characteristic.
- Automatic Hot Start to improve the arc striking with the most difficult electrodes.
- Electrode Antisticking function
|
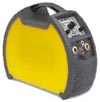
Rainbow 170 HF
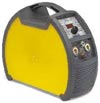
Rainbow 200 HF
|
 |
RAINBOW 170 HF and digital control RAINBOW 200 HF represents the latest evolution of inverter DC welding machines.
These powerful 100 KHz power sources, based on the very latest IGBT technology and fitted with flat transformer, can be used for TIG welding of any metal, excluding aluminium and its alloys. RAINBOW 170 and 200 HF, which also perform very well in MMA welding , thanks to their light and compact size and excellent welding characteristics, are the ideal solution for maintenance, assembly and light fabrication works.
Features:
- Innovative and compact design
- Shock-proof plastic main structure
- Control panel protected against accidental impact
- Robust handle built-in into the chassis
- Reduced weight and dimensions, easy-to-carry
- Precise and efficient TIG arc striking by high frequency
- High performance on thin metal sheets
- Standard equipped with pulse mode integrated into the control with available "EASY PULSE" facility (RAINBOW 200 HF)
- Digital control of all the welding parameters with the ability to store 9 personalised programs (RAINBOW 200 HF)
- Automatic compensation for mains voltage fluctuations within + 15% - 20%
- Low energy consumption and high efficiency
|
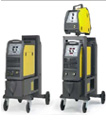 |
 |
The synergic multifunction DIGITECH power sources, based
on the most modern IGBT inverter technology and fully digital
controlled, allow premium welding quality in both MIG-MAG
and in Pulsed and Dual-Pulsed MIG on all materials and particularly
on stainless steel, aluminium and galvanized steel, by minimizing
any reworking job thanks to their spatter free welding. Technologically
advanced, easy-to-use, DIGITECH's represent the ideal solution
for any application requiring high precision and repeatability
of the achieved results. The DIGITECH's versatility allows
the operator achieve optimal performances both in TIG by "lift"
mode striking and in MMA welding.
DIGITECH 400 models are supplied with separate wire feeder,
whilst DIGITECH 300 Compact is designed with built-in wire
feeder.
Features:
- Synergic digital control of all the welding parameters.
- Spatter free exceptional welding characteristics in both
MIG/MAG and PULSED MIG on any material and with any gas
- High welding performance in both MMA and TIG by "Lift"
mode striking
- Ability to store personalized welding programs
- "Energy Saving" function to operate the power
source cooling fan and the torch water cooling only when
necessary.
- Monitoring and repeatability of the welding parameters,
which can be printed
- User friendly and easy-to-use selection and recalling
of the parameters and welding programs
- Low energy consumption
- Remote parameter adjustment directly from TA 4 feeder
- Auto-diagnostic feature for trouble shooting
- Initial and crater welding cycle control
- The use of special MIG torches permits the remote control
of the welding parameters directly from the torch
- Innovative and user friendly design
- Metallic main structure with shock-proof plastic front
frames
- Control panel protected against accidental impact
- Robust handles built into the chassis
- Sloping front control panel, easy to read and adjust and
highly visible from any direction
|
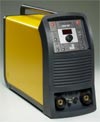 |
 |
Based on the very latest IGBT inverter technology, TIG power sources with high frequency arc striking of the MATRIX series are equipped with an innovative digital panel for the complete control of all the welding parameters.
The excellent technical characteristics of these welding machines, coupled with the feature of digital control, allow high quality TIG welding, suitable for the toughest industrial applications and maintenance.
These highly advanced technology power sources are robust and user friendly: MATRIX HF’s, DC output only, enable TIG welding of mild and stainless steel, copper and its alloy.
MATRIX series power sources also offer excellent performance also in MMA welding with the most difficult basic and cellulosic electrodes.
Features:
- Compact and innovative design
- Metallic main structure with shock-proof plastic front panel
- Control panel protected against accidental impact
- Robust handle integrated into the chassis
- Reduced weight and size, easy-to-carry
- Digital control of all the welding parameters
- Standard equipped with pulse mode integrated into the control with available "easy-pulse" facility
- Excellent TIG welding characteristics
- High frequency arc striking, precise and efficient even from long distance
- High performance on thin metal sheets
- Automatic compensation for mains voltage fluctuations within +15% -20%
- Very good MMA welding characteristics with any type of electrodes
- Easy-to-use
- Low energy consumption
- Use of special TIG torches will enable the remote control of the welding parameters directly from the torch
|
 |
 |
Based on the very latest IGBT inverter technology, TIG power sources with high frequency arc striking of the MATRIX series are equipped with an innovative digital panel for the complete control of all the welding parameters.
The excellent technical characteristics of these welding machines, coupled with the feature of digital control, allow high quality TIG welding, suitable for the toughest industrial applications and maintenance.
These highly advanced technology power sources are robust and user friendly: MATRIX AC/DC’s can also be used for TIG welding of all metals, including aluminium and its alloys.
MATRIX 200 AC/DC, single phase mains input, is the ideal solution for maintenance works.
MATRIX series power sources also offer excellent performance also in MMA welding with the most difficult basic and cellulosic electrodes.
Features:
- Compact and innovative design
- Metallic main structure with shock-proof plastic front panel
- Control panel protected against accidental impact
- Robust handle integrated into the chassis
- Reduced weight and size, easy-to-carry
- Digital control of all the welding parameters
- Standard equipped with pulse mode integrated into the control with available "easy-pulse" facility
- Excellent TIG welding characteristics
- High frequency arc striking, precise and efficient even from long distance
- High performance on thin metal sheets
- Automatic compensation for mains voltage fluctuations within +15% -20%
- Very good MMA welding characteristics with any type of electrodes
- Easy-to-use
- Low energy consumption
- Use of special TIG torches will enable the remote control of the welding parameters directly from the torch
|
 |
 |
PLASMA PLUS 55, for compressed air cutting, provides a low cost and efficient cutting system to be used on any metal, from 0,5 to 15 mm. It is suitable for light/medium industrial applications. To ensure the safety of the operator, each model is provided with an electric device on the torch.
Features:
- Torch with Pilot arc
- Easy operation and high cutting capacity (15mm max)
- Cutting and protection cycle displayed by leds
- Low energy consumption (16 A)
- Low air consumption (150 L/Min)
- Working cycle monitorized by Leds
|
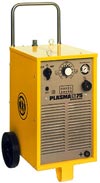 |
 |
PLASMA PLUS 75 equipment, for compressed air cutting, provides a low cost and efficient cutting system to be used on any metal, from 0,5 to 22 mm. It is suitable for light/medium industrial applications. To ensure the safety of the operator, each model is provided with an electric device on the torch.
Features:
- Torch with HF and Pilot Arc
- Electronic adjustment of cutting current
- Cutting and protection cycle displayed by leds
- Complete stability of cutting parameters within +/- 10% mains voltage
- Reduced cutting fumes
- Arc parameters control unit for an excellent arc quality
|
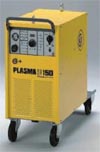 |
 |
This powerful three-phase equipment, based on the latest evolution of the consolidated Thyristor technology, grants reliability and safety in any work condition. The innovating cutting current control system Total Wave Control TWC and the electronic adjustment allow to select the very best parameters in any application, granting superior cutting quality on any thickness and material . Plasma Plus 150 E enables the utilisation of different amperage torches, air or water cooled, by also automatically recognizing the used torch and changing the range of cutting currents for each fitted torch. The control panel helps the operator by automatically indicating the correct tip diameter to be used depending on both used torch and preselected cutting current.
Features:
- Digital panel for preselection and reading of the cutting current
- Continuous cutting current adjustment
- Possibility of using different amperage torches
- Identification of the used torch and automatic cutting current range change from 25A - 75A to 25A - 150A
- Cutting parameters stability within ± 10% mains voltage fluctuations
- Filter and regulator group with air impurity automatic expulsion
- Contact cutting possibility with currents below 50A without sliding blocks or other spacers
- Possibility of use on an automatic cutting equipment
- Automatic fan motor switching off 9 minutes after cutting operation is over, to reduce airborne contaminants drawn into the equipment
|

|
|
|
|